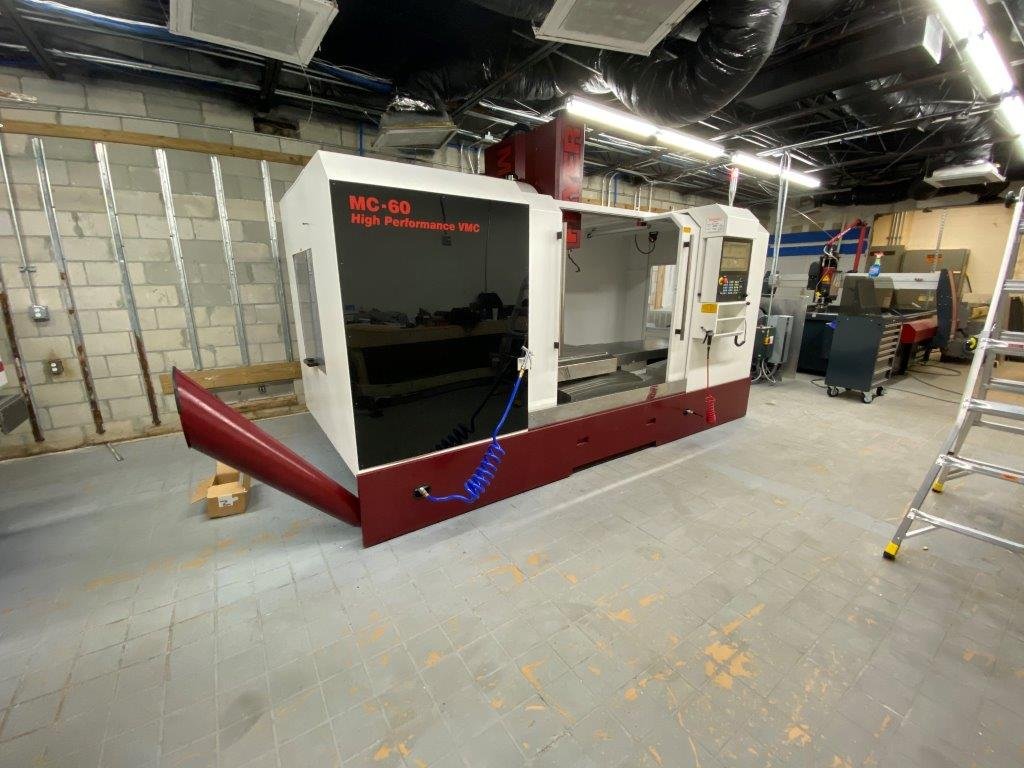
Machining & Programming
VISION MT programmers use stp, prt, Autodesk Inventor CAD/CAM, FeatureCAM and other 3D file formats to create and program machines.
Machinists evaluate drawings for necessary tooling and fixturing that will preserve dimensional accuracy based on the geometry of a part and the dimensions, tolerances, and hole patterns instructed by the print.
Parts move from the waterjet and CNC milling machines though bend and a combination of Alodine, prime, paint and silkscreen before heading to final assembly. Engineers and QA conduct in-process inspection throughout and final inspection before parts are sent for aircraft installation. Engineers and QA conduct in-process inspection before parts head to finish for a combination of alodine, prime, paint and silkscreen. Another round of inspection and part marking takes place before the part is sent to Finished Goods.
VISION MT maintains various sizes of sheet metal, extrusion and common hardware enabling us to support customer design changes and rapid turn requests quickly - often to be brought to a waiting aircraft.
Our structural shop has equipment to achieve the highest level of machining and programming accuracy, including capability to work with aluminum, steel, titanium and plastics, including:
Fryer MC-60 CNC - 3 axis machine with a reinshaw probe/expanded memory/3D graphics simulation and max spindle-speed of 8k RPM
Fryer MB-14Q CNC - 3 axis/rigid tapping/handwheel run function/dxf file import and 3D graphics simulation
HAAS CNC - 40 X 20 with a 4th axis rotary accessory and 10,000 rpm spindle speed
Fryer MC-60 CNC - 3 axis machine with a reinshaw probe/expanded memory/3D graphics simulation and max spindle-speed of 8k RPM
Fryer MB-14Q CNC - 3 axis/rigid tapping/handwheel run function/dxf file import and 3D graphics simulation
HAAS CNC - 40 X 20 with a 4th axis rotary accessory and 10,000 rpm spindle speed
Waterjet - Maxiem 1530 with bed travel , 3 Axis cutting head, 2 ton chiller, bulk abrasive hopper, with bed travel of 96” X 48” and 500 ipm traverse speed with real-time closed loop positioning feedback for accuracy & performance
CNC Press Brake – Coastone electric Pressbrake with steel construction USHB44-6 Hydraulic with 78.7” working table and 44 ton working pressure. Ram deflection adjustment, mechanical depth control, torsion bar for parallelism and 3 speed bending cycle.
Rotating Lift – RTMX 30 Roto max
CMM – XM series handheld scanner that creates a 3D mesh for part to CAD comparison
3D Printer - Raise 3D Pro 2 and Bambulab
Welding -Syncrowave 250 DX TIGrunner 3CS and Torch kit
Heat Treat- Heat Treating, Annealing and Aging temperatures up to 1200°F and qualifies as Class 1 or Class 2 (AMS2750F).


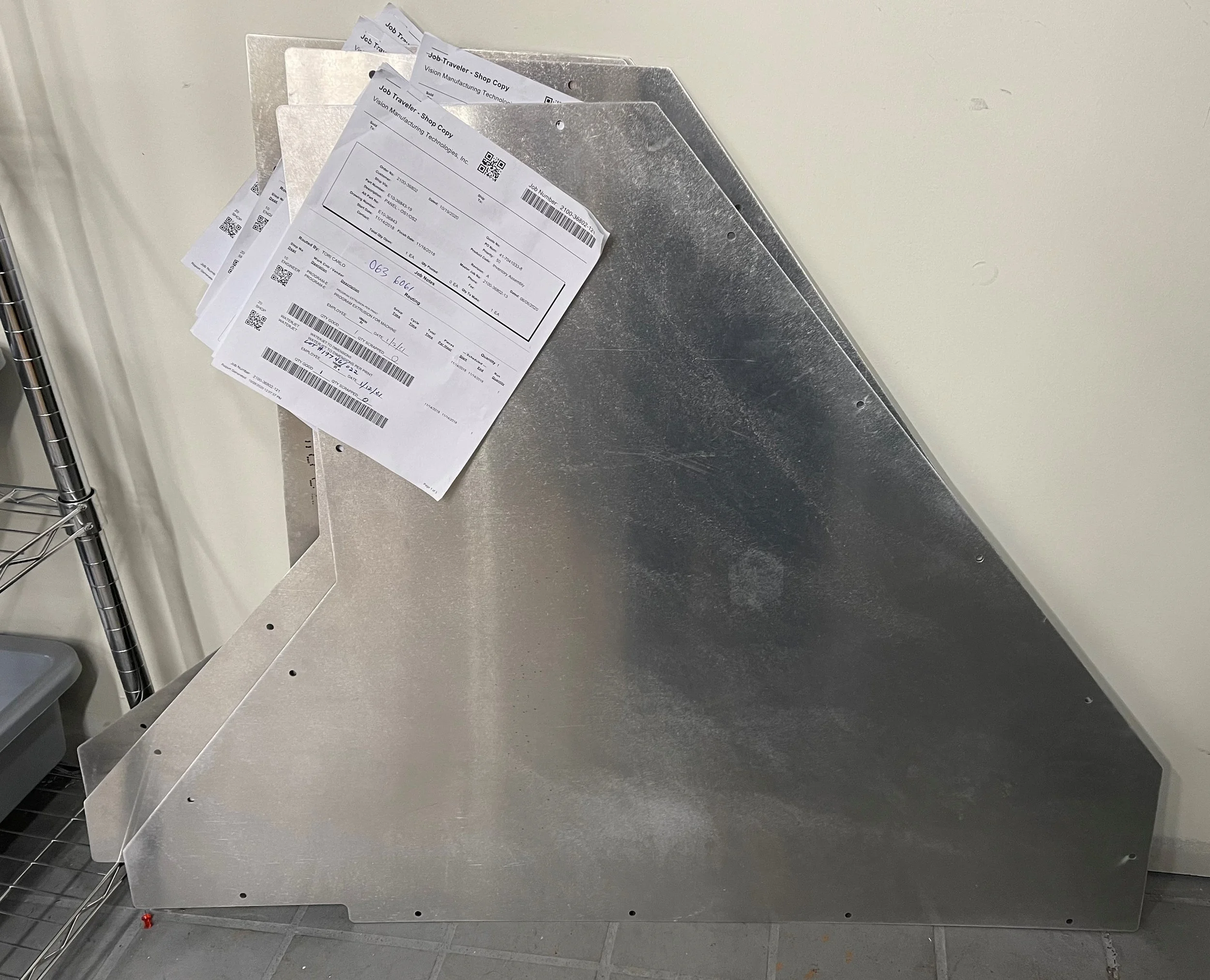

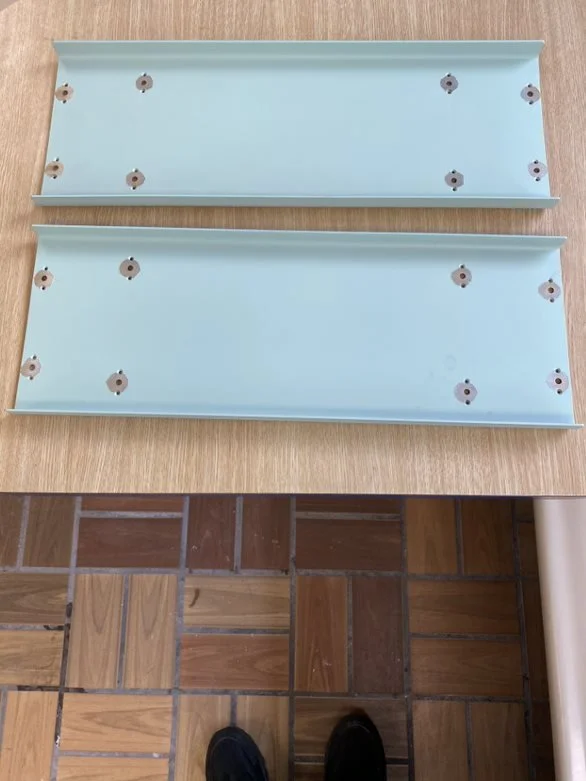


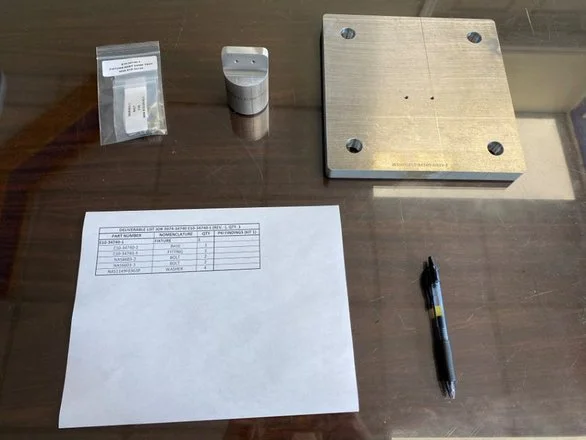
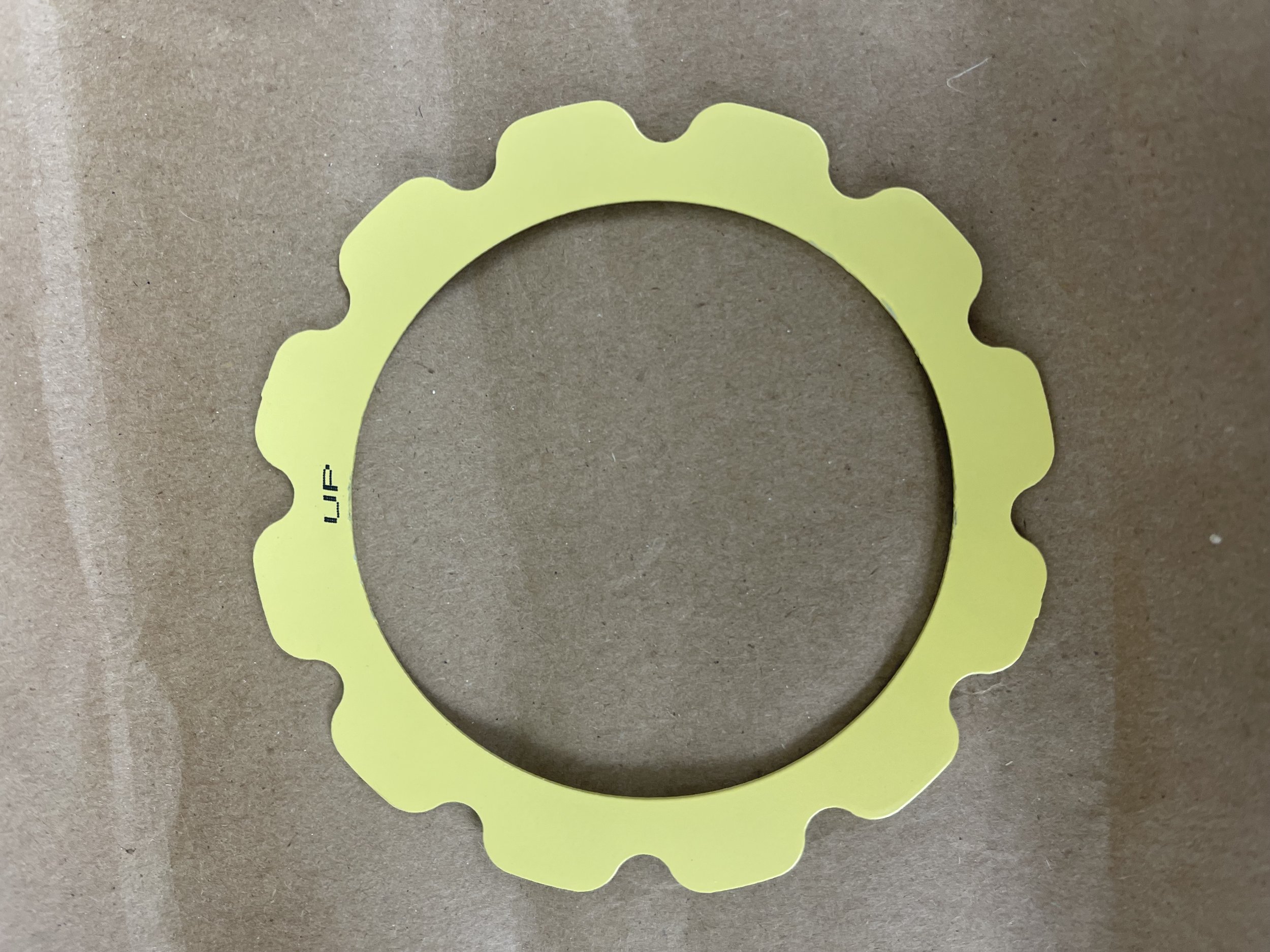
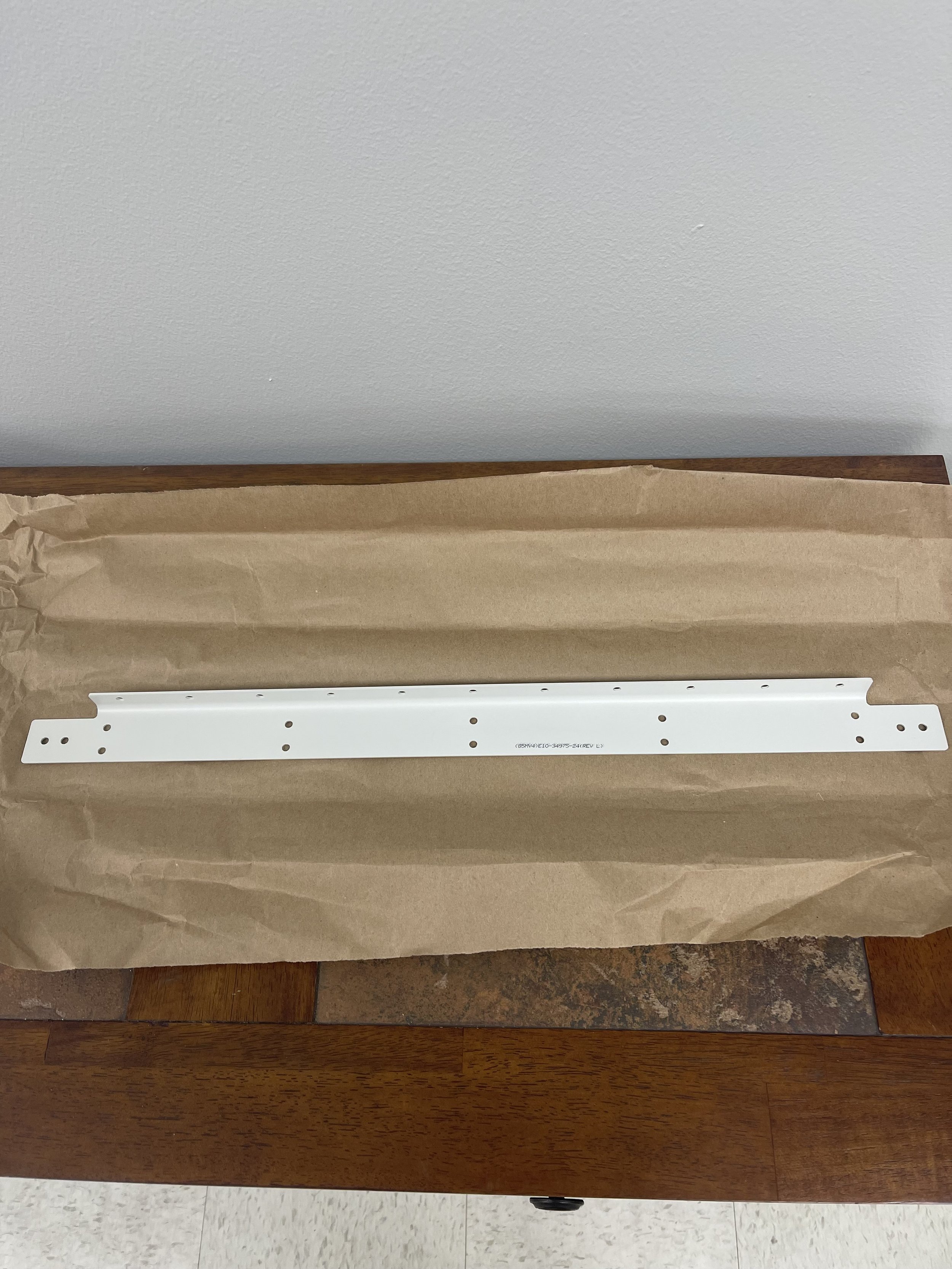
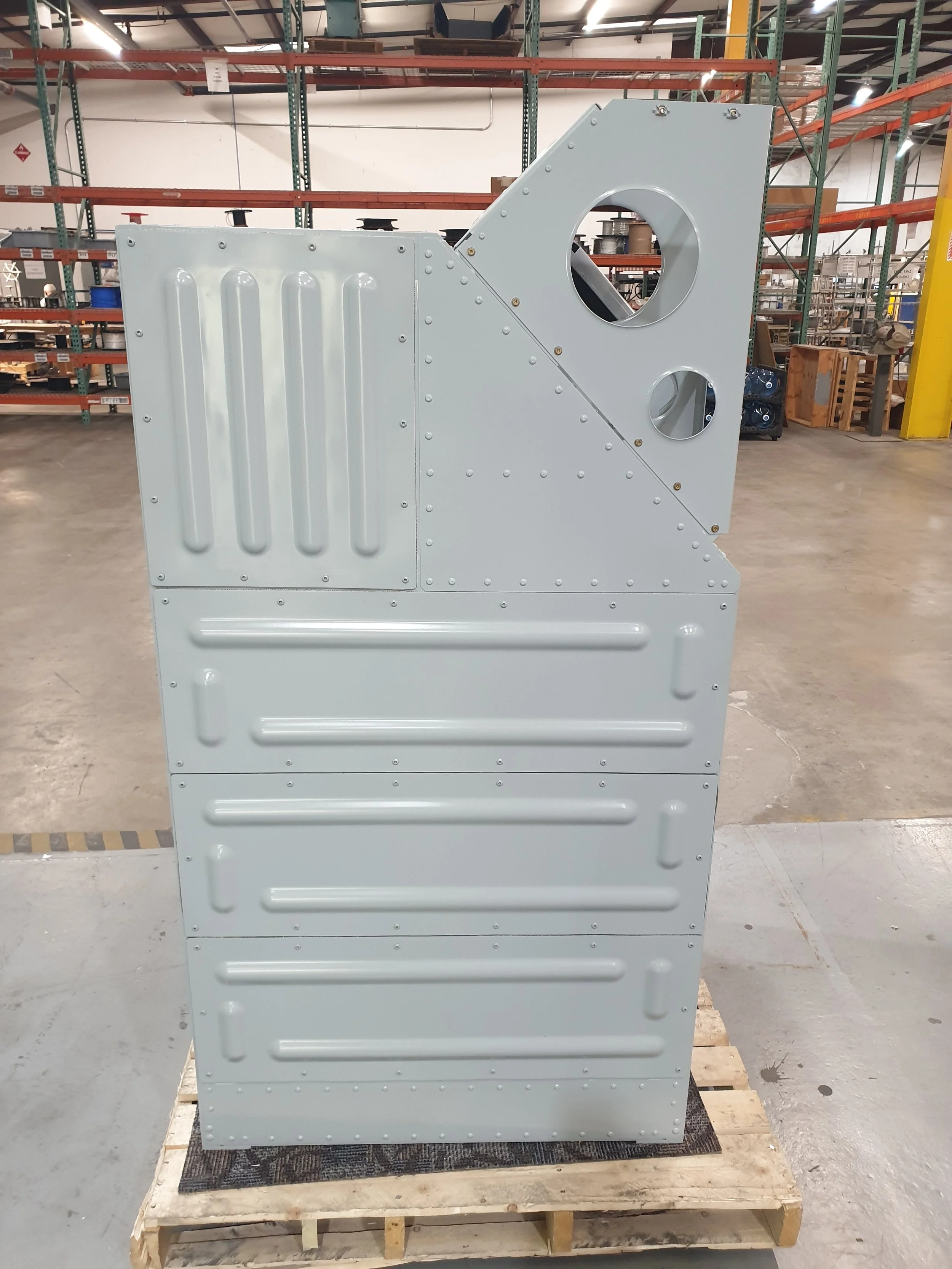
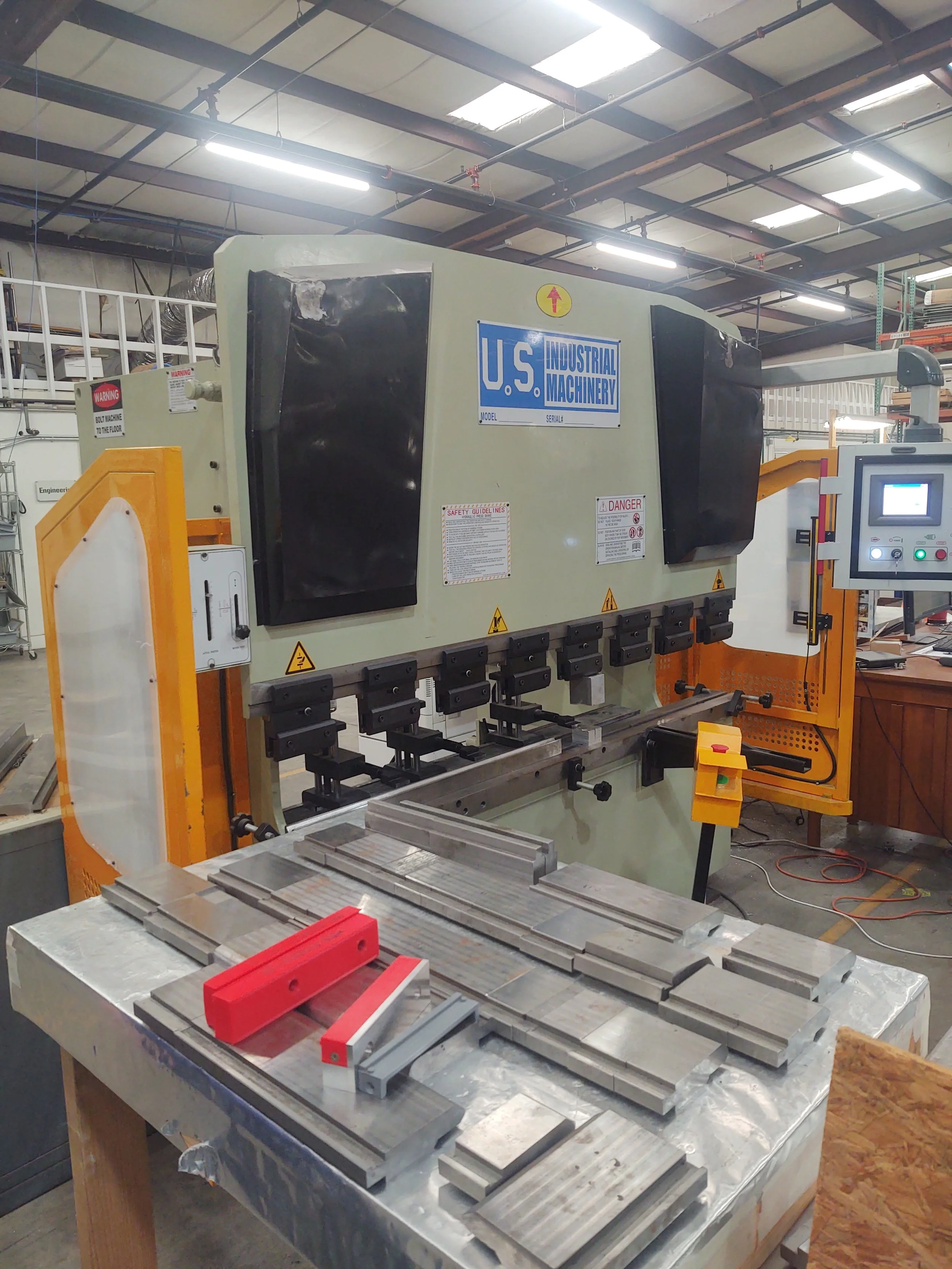
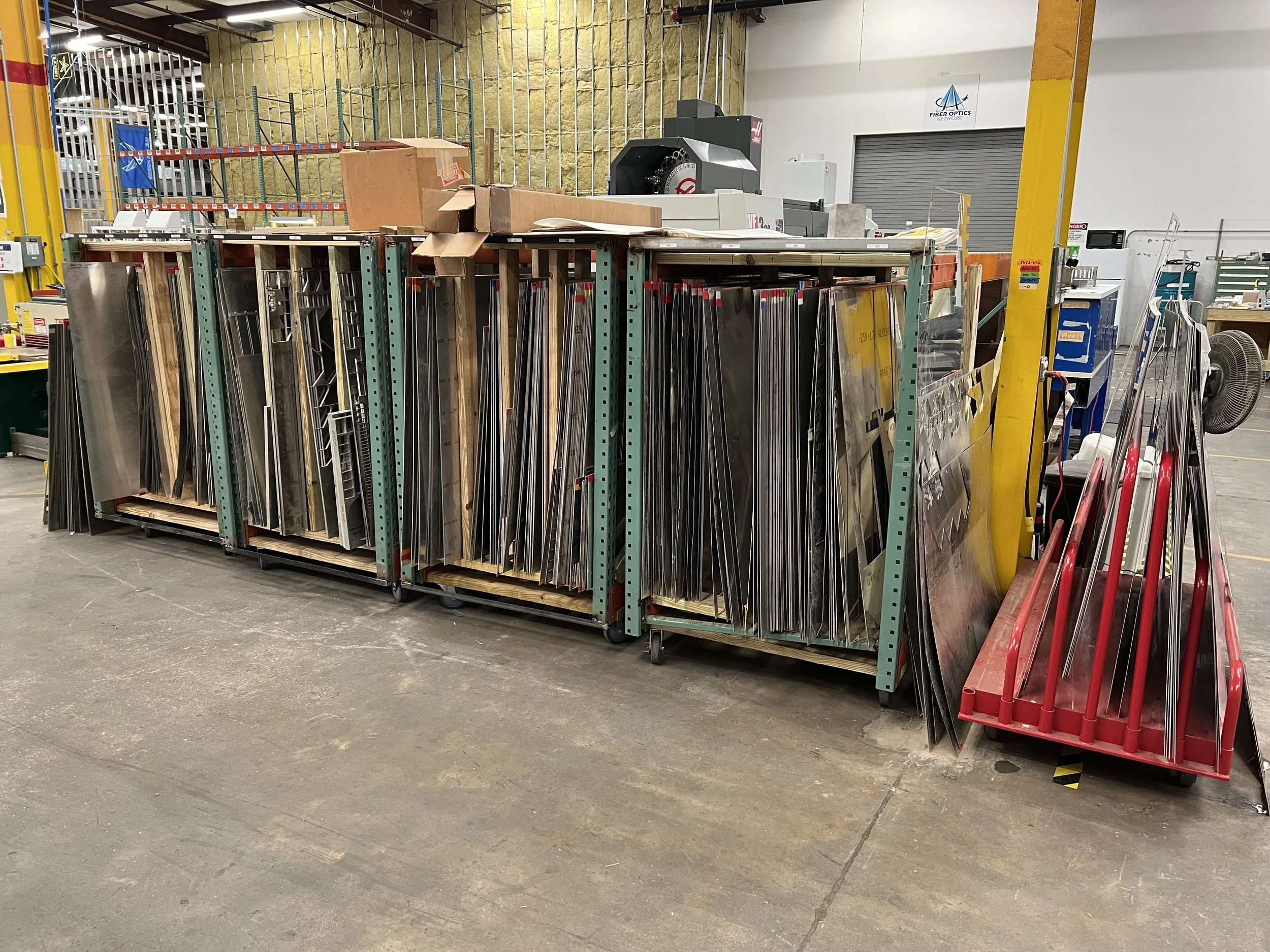
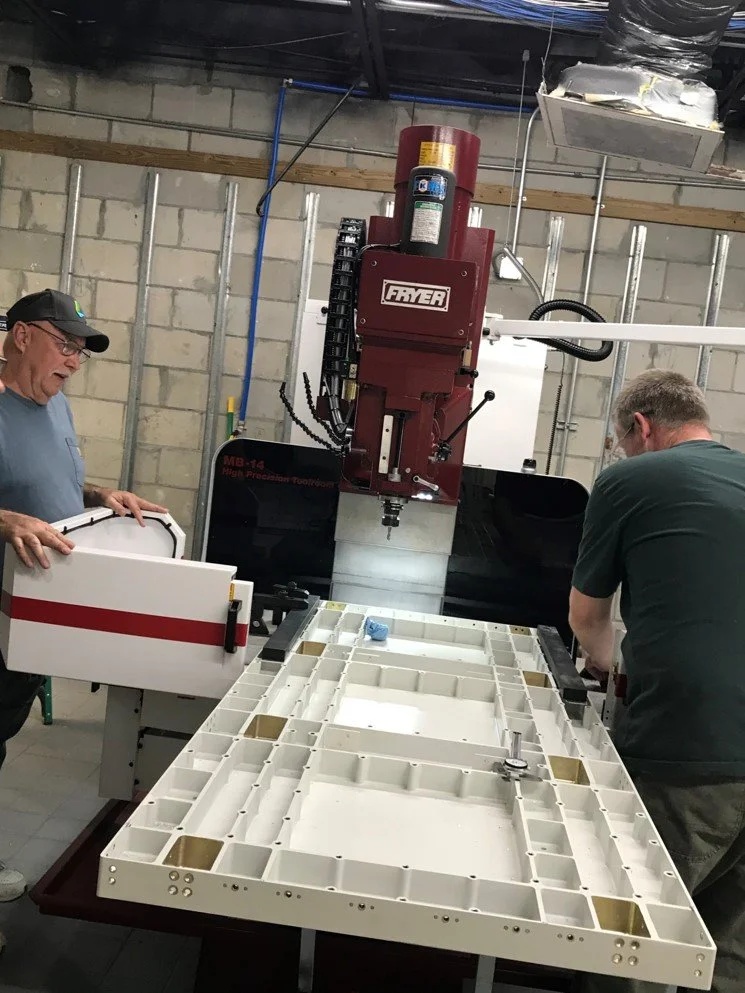
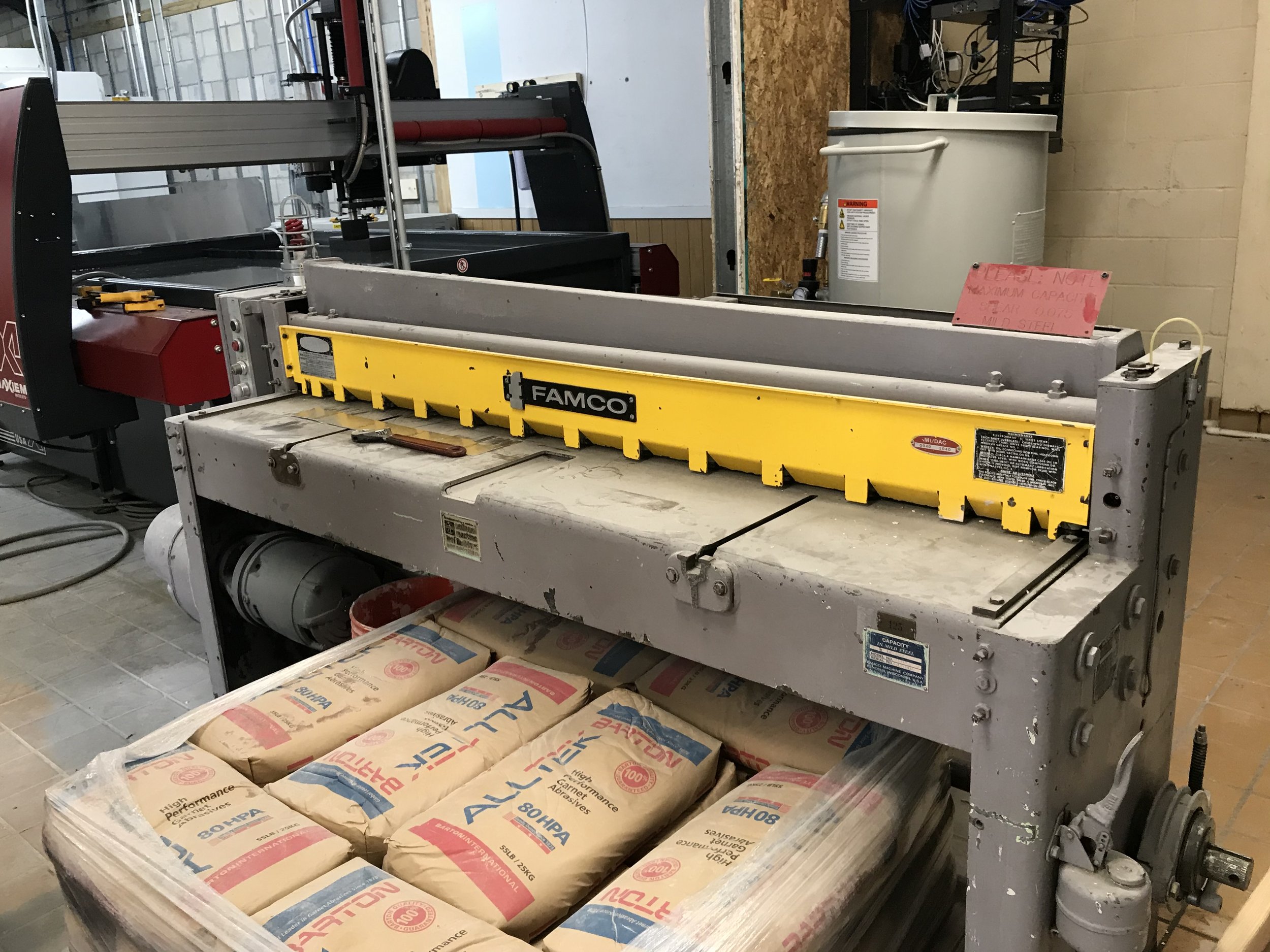

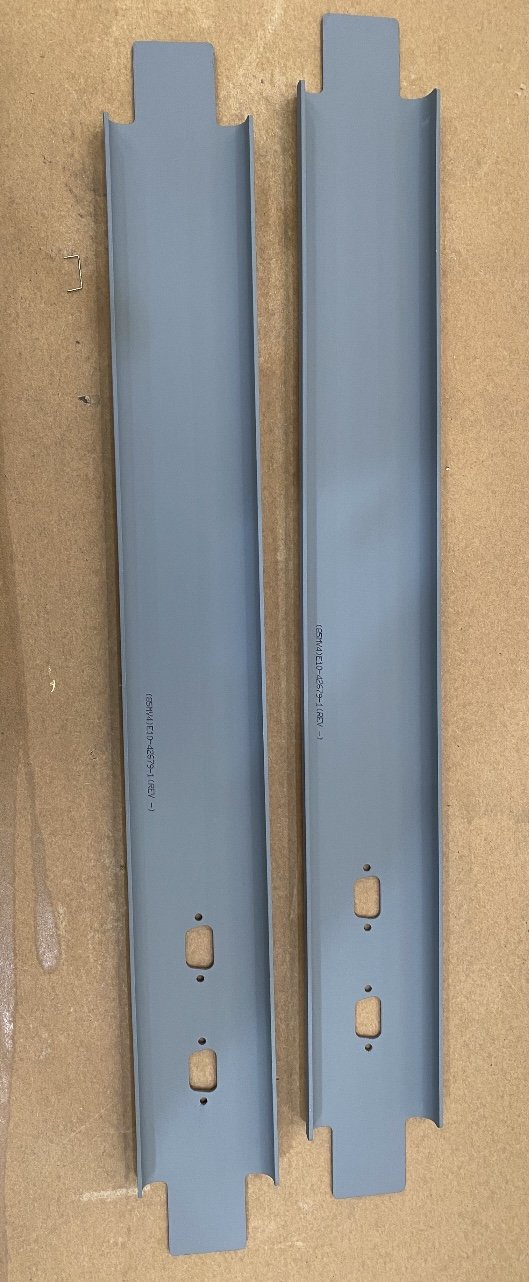
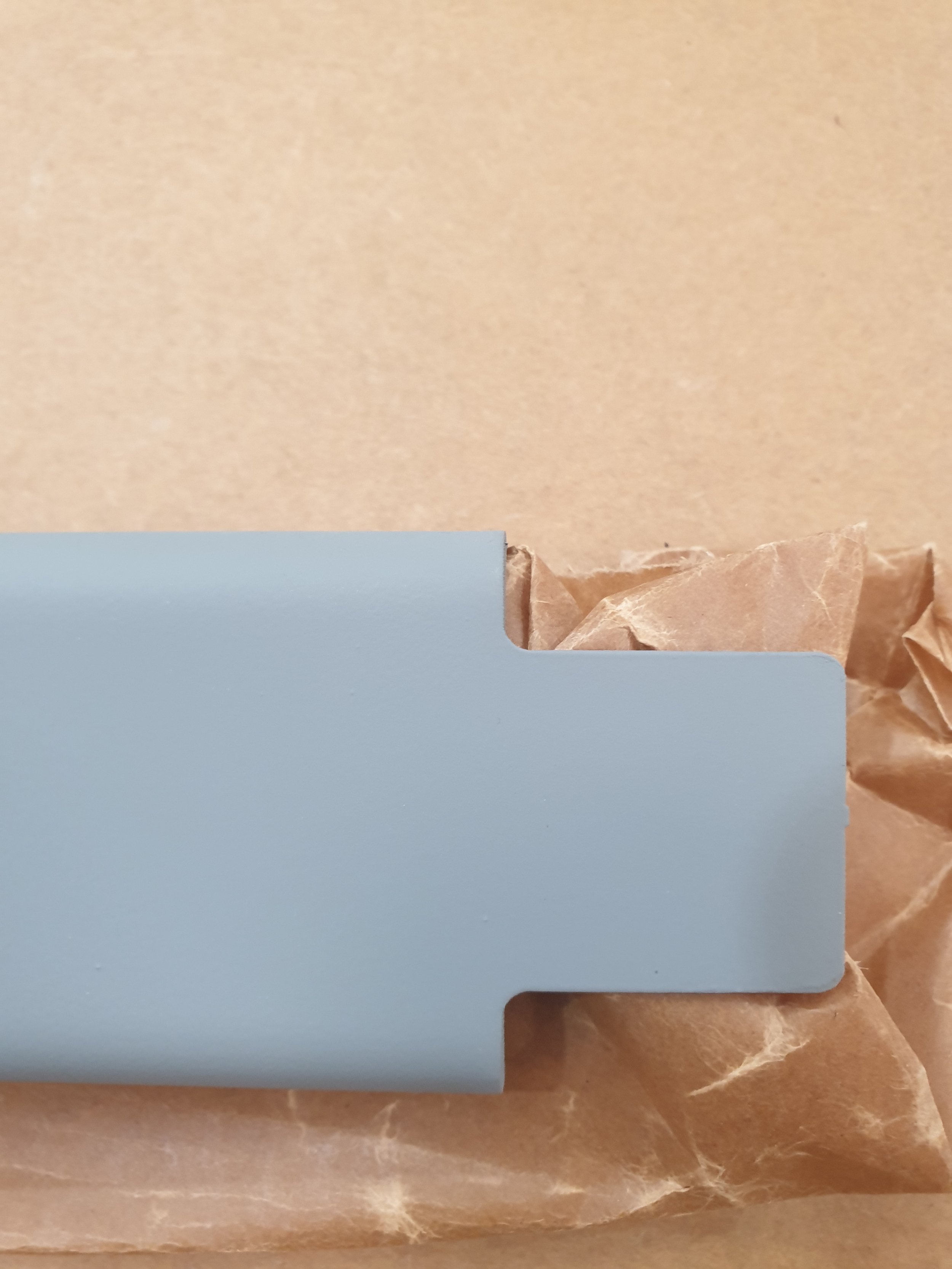
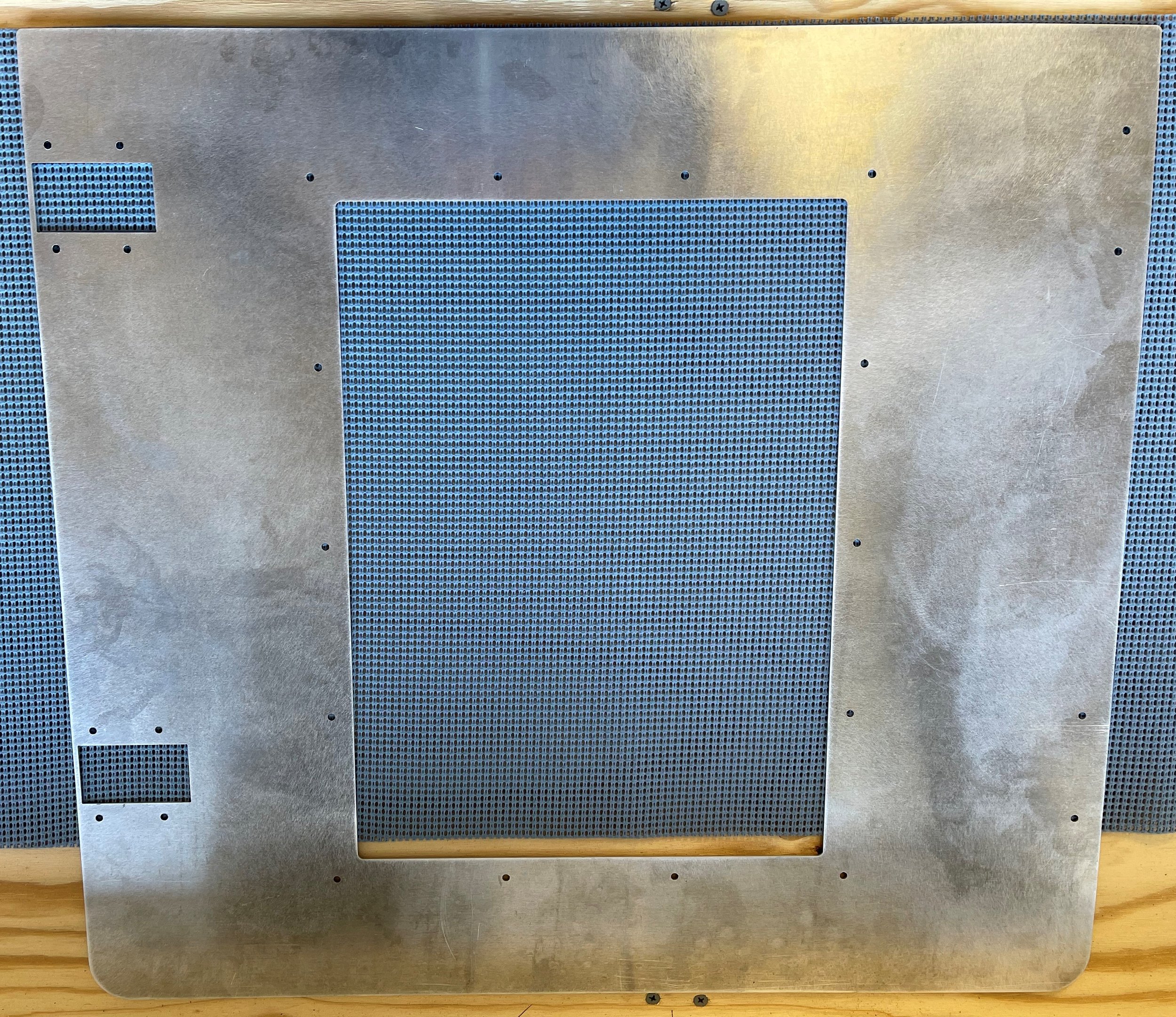
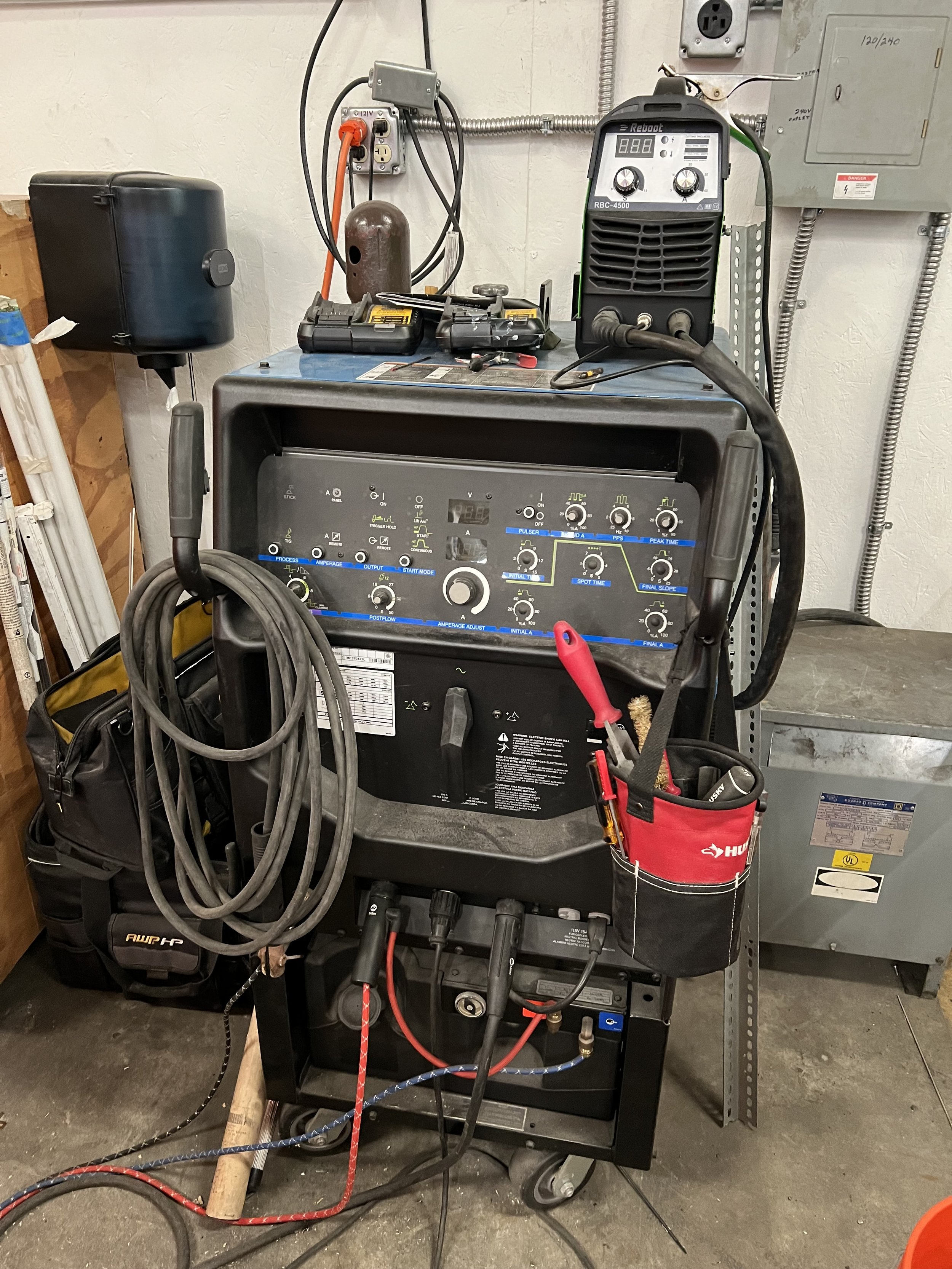
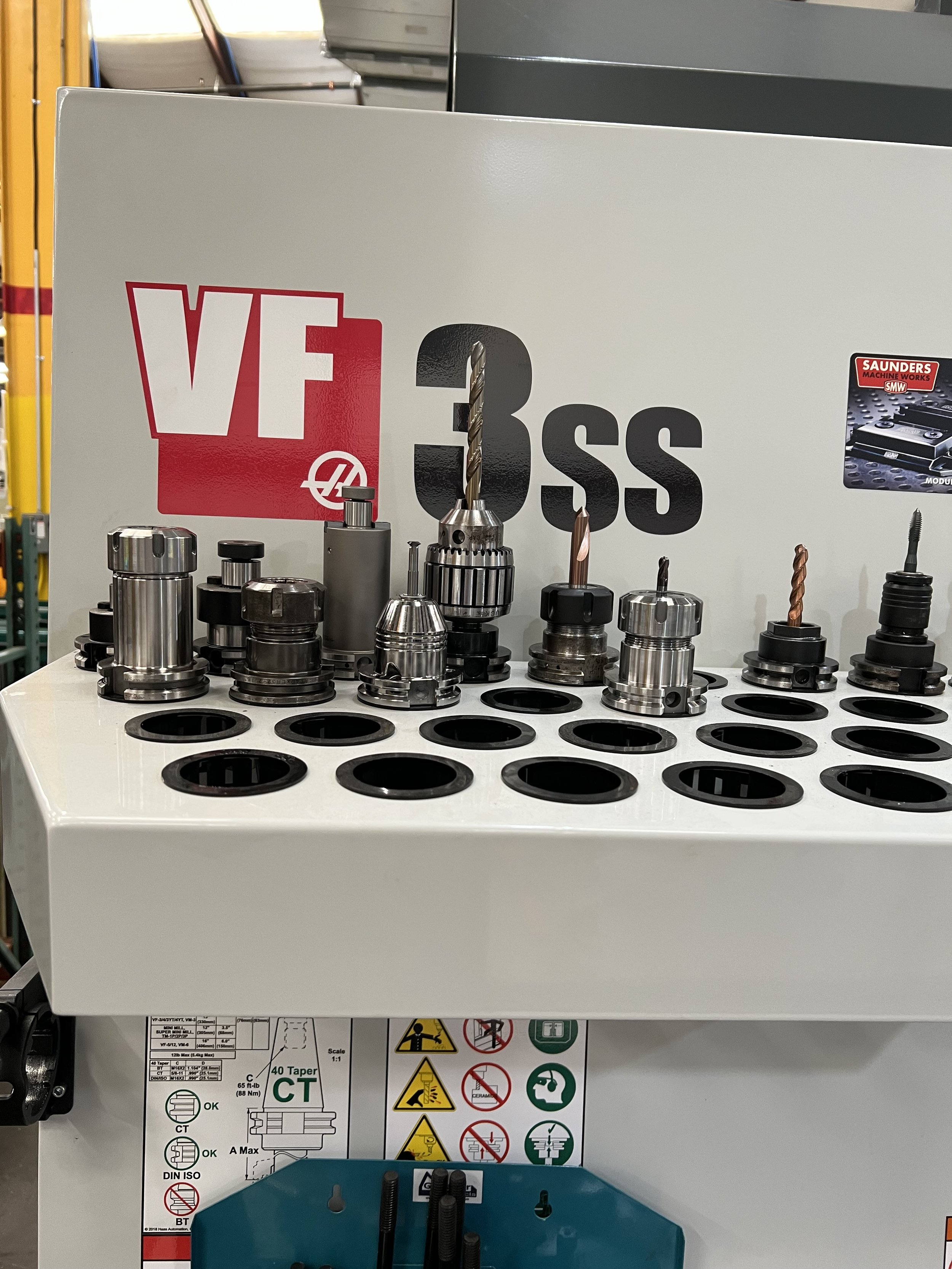
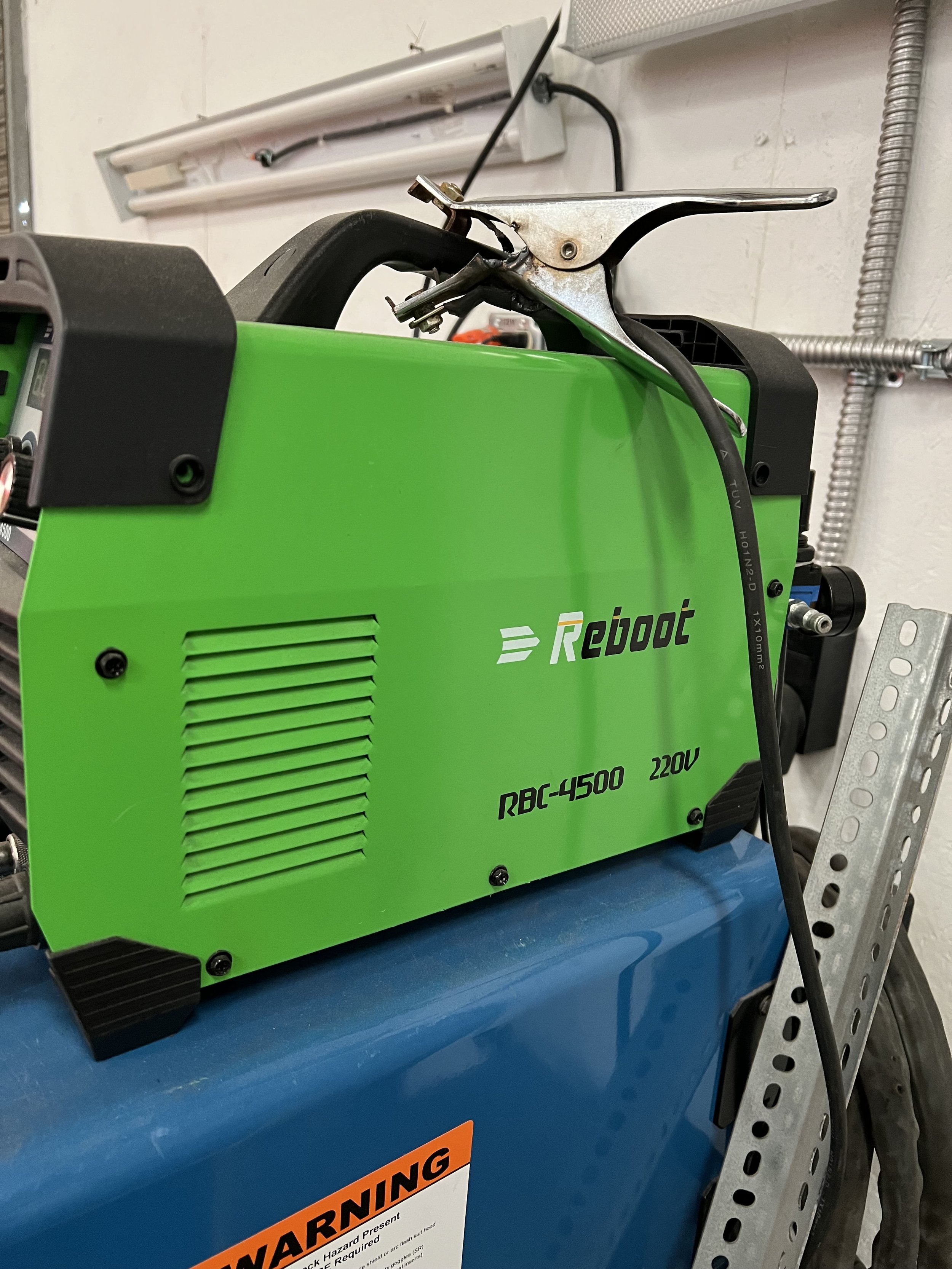
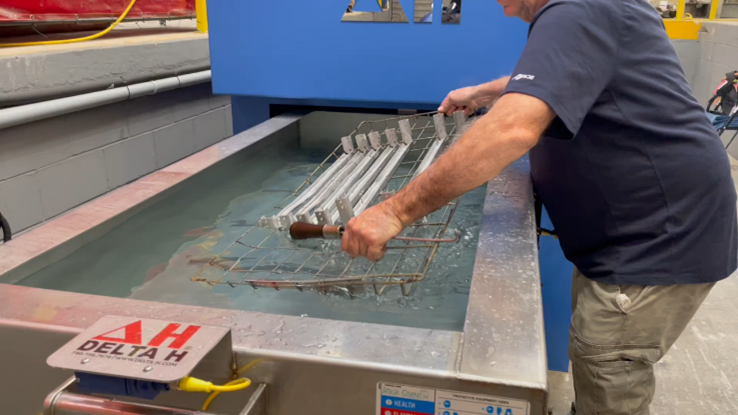
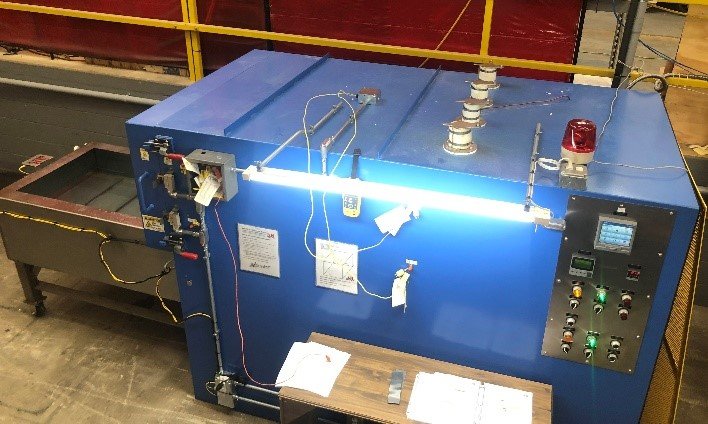
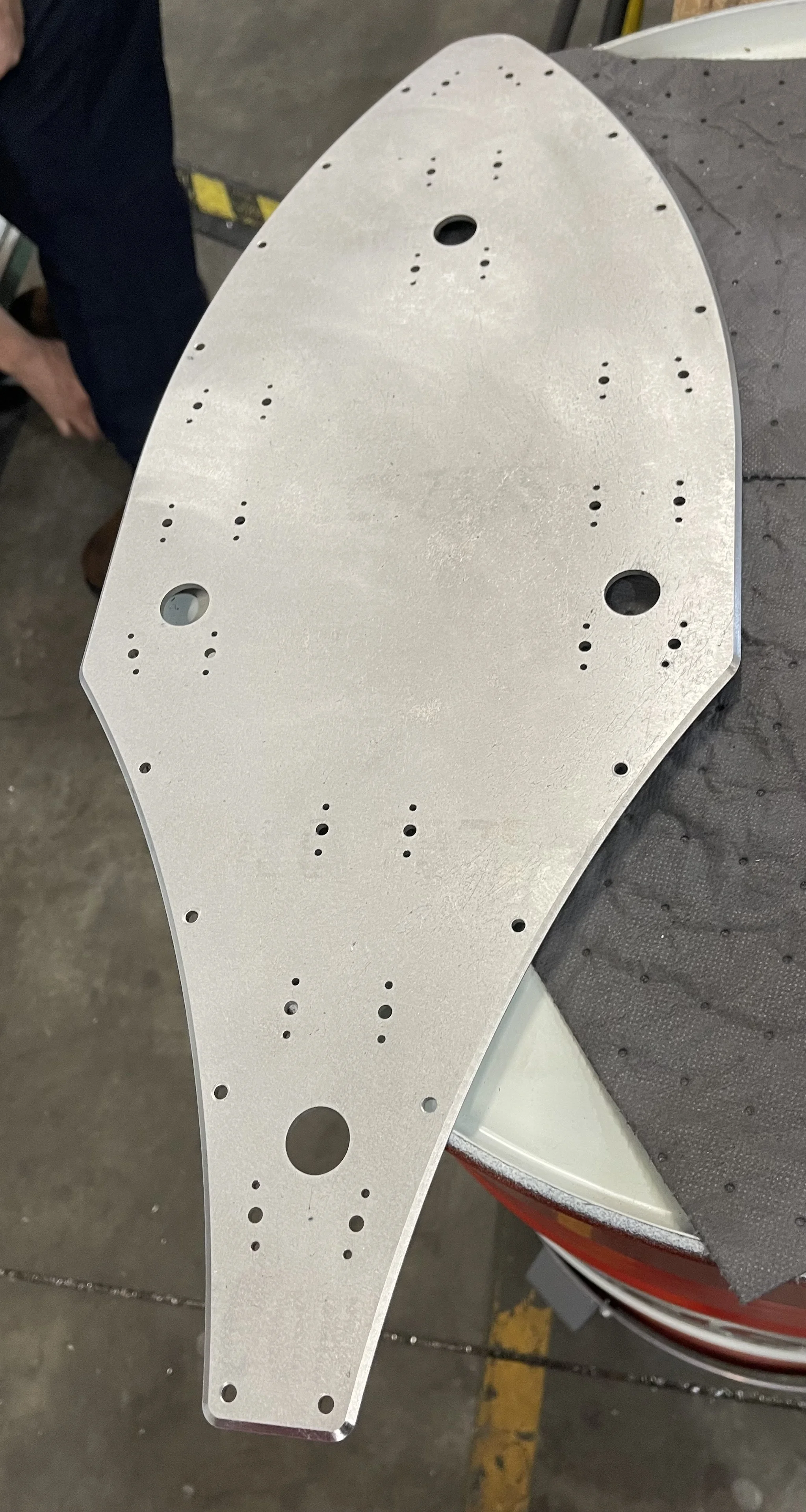